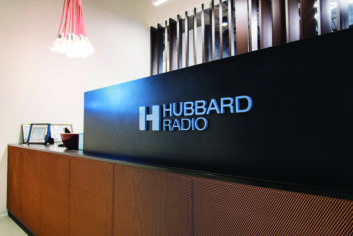
Those of us who have participated in one know that a station move can produce the most stressful times in our careers, regardless of market size. Recently, Hubbard Radio took on such a project for its Chicago radio stations, consolidating FM stations WTMX “The Mix,” WSHE and WDRV “The Drive.” The project was directed by Kent Lewin, chief engineer of the cluster, and facilitated by integrator RadioDNA, headed by Rob Goldberg.
PHYSICAL AND TIME CONSTRAINTS
As with so many projects of this sort, the end of a lease precipitated the move. In this case, WDRV was coming to the end of its lease at the John Hancock Center building, while WTMX and WSHE were already located about a mile away at the Prudential Building.
Hubbard Director of Engineering Dave Garner said, “The Drive was on a very short fuse as far as its existing lease, and it had to be out by the end of last April [2018] so it was a real tight schedule. That was the moving force, and the timing was such that we had to work all the other renovations around moving the Drive into Prudential.”
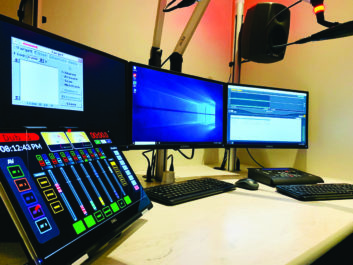
The company decided to completely revamp the Prudential facility. Before WDRV moved over, a series of temporary moves needed to be accomplished.
“It was really like musical chairs,” said Garner. “They took a large office and moved The Mix into that area; and after that, the rebuild project was kind of like dominoes. We got The Drive in there, and it was just moving things around — moving studios from one station to another — in order to accommodate them. We actually created production rooms in some new offices. In other words, somebody’s office — like a programming office, for example — became a production studio, and that happened numerous times during the reconfiguration.”
All the pieces came together. Through careful planning and timely execution, the team completed the project on time, with just a few days left on the calendar to spare.
“It was, to say the least, quite a project,” Garner said.
NEW CONSOLES AND ROUTER SYSTEM
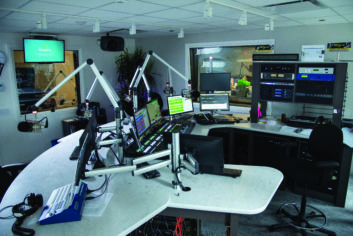
As part of the entire revamping of the Chicago facility, the three stations were re-equipped using the Wheatstone AoIP system WheatNet. For this project, radioDNA built out 13 studios: on-air studios for WSHE, WDRV and WTMX plus a back-up on-air studio that can be used by any of the stations; three large-scale production rooms; three dubbing studios (i.e., less-capable production rooms); and three call-screen/producer booths.
The four on-air studios have Wheatstone’s 37-module LXE frame, with 25 motorized faders. “It’s just a monster,” said radioDNA’s Goldberg about the console. “It was pretty cool unboxing that huge coffin, as you can imagine.”
The air studios for WSHE, WDRV and back-up on-air are fixed-position, stand-up designs. However, according to Goldberg, the console in the WTMX on-air studio has a unique setup, designed and built by Studio Technology.
“It actually is a motorized countertop, so the whole thing can go from basically sit-down to higher than stand-up. A lot of extra engineering went into that — as you can imagine, the huge countertop for a multi-person morning show and a 37-module console. The countertop is big and heavy. It has eight motorized legs to lift and stabilize the thing, which is pretty cool.”
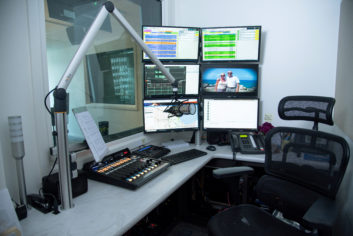
[Hubbard Radio Testing All-Digital AM on Maryland’s WWFD]
The big production studios use Wheatstone L-12s. Goldberg said, “Each of the large production studios has Pro Tools and Wheatstone’s VoxPro — actually every studio in the new facility has VoxPro, so there are 13, all told. We also included near-field monitoring using Genelec speakers.”
The call-screen/producer studios use Wheatstone L-8s, and each studio has direct line of sight to its associated on-air studio.
“We just didn’t have the room (in the group of the three smallest studios) or the countertop space to put a control surface. There just wouldn’t have been any work room; they’re very small. So we built the control surfaces on a Microsoft Surface Touch Pad, using Wheatstone ScreenBuilder.” ScreenBuilder is a software tool that lets the end-user build control, routing and monitoring interfaces on a PC or touchscreen tablet to create virtual surfaces.
“There’s a boom arm that holds some monitors, a mic boom and mic status [by way of a visual indicator], and they have a VoxPro, BE AudioVault and an Adobe editor machine in this small studio. We had to do things efficiently. ScreenBuilder works great.”
CUSTOM FEATURES
As with any studio build, this one includes custom features.
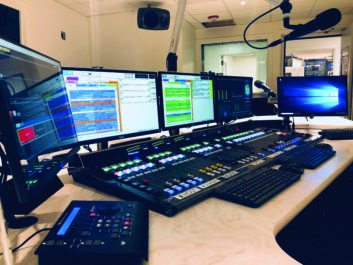
“For WTMX, we have two screener/producer studios and both have talkback in to the main studio, and they can talk to each other as well,” Goldberg said. “We added logic to indicate if a studio’s live or not — and there’s a lot of talking back and forth, with five people in all, including the screeners and the co-hosts for WTMX. We also have another one of the little booth studios, which can also function as a screener studio, that has talkback capability as well, for phone screening and whatnot.”
The screener/producer studios also have separate indications for when local mics are live on-air, or just live in the room. “We did little things like that, to just make it nice and easy for the operator so they can know when they’re live and when they’re not,” said Goldberg.
He added that Hubbard’s Market Chief Kent Lewin had a stringent set of requirements with respect to system redundancy.
[Who’s Buying What: WTOP Uses EV Mics at Big New Facility]
“As radio engineers, we all are into backup systems and redundancy. Kent really takes that to the next level with everything. With the AudioVault, every audio output coming into a control surface comes from a different audio server — so you could actually completely lose one server, and all that would happen is that one channel would be missing.
“In addition to that, he actually breaks it out so the music comes from one control machine and the stop sets come from another. This created unique challenges in how we were going to control those machines. Previously they used custom relay boxes that did some neat things from their old boards and talked to the automation system. We did it all through programming directly from the surface to the AudioVault for all four music decks and all four spot decks. We programmed the cue button so that when you press it, it starts the first 30 seconds of the song; when we turn the cue off it stops the deck and cues it back up.”
THE RACK ROOM
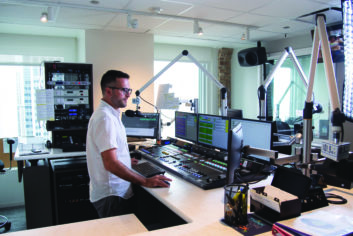
Due to time constraints, a rebuild of the stations’ rack room will be revisited later.
“Time was a little bit tight with all the moves, so we didn’t finish the rack room,” said Goldberg. “We’re actually going to come back and revamp it with all new equipment racks, and we’ll be taking out old gear to make room for the new.”
The blade count, as it stands now, is in the upper 70s, according to Rob.
“There’s plenty of growth — we didn’t use every I/O from each blade. We like to put blades where gear is. For example, Studio Technology builds these nice roll-around racks that come out from underneath the furniture. We have minimal cable going to these roll-out racks and we like to keep all of the audio interconnects within that rack if at all possible, not having to go out of a rack and then back.
“Our goal is to keep things organized and neat, so when you pull out the rack you have everything that was installed, or anything that needs troubleshooting, right in front of you.”
Though big studio projects like the one Hubbard has accomplished in Chicago can produce the most stressful times in your career, the upside is that, afterwards, you’ll likely have had some of the proudest moments of your life. Projects such as this offer a rare — perhaps once-in-a-career — chance to make a real difference in an operation or in a company.
Hubbard Chicago equipment list
- 25-Seven Systems PDM
- Avid Pro Tools
- Benchmark SPM-2 program meters
- Broadcast Electronics AudioVAULT automation software
- Denon DN-700R SD/USB networkable SD/USB recorder
- Fostex RM-3 powered rackmount audio monitors
- Genelec powered monitor speakers
- Studio Technology custom furniture
- Tascam 500B CD players
- Wheatstone WheatNet AoIP system
- Wheatstone L8, L12, LXE consoles
- Wheatstone VoxPro audio software
- Yellowtec m!ka mic booms, monitor arms
Doug Irwin is the VP of engineering for the Los Angeles Region of iHeartMedia.